Ungkap Rahasia! Tips Menang Slot Hoki Hanya di Kingkong39
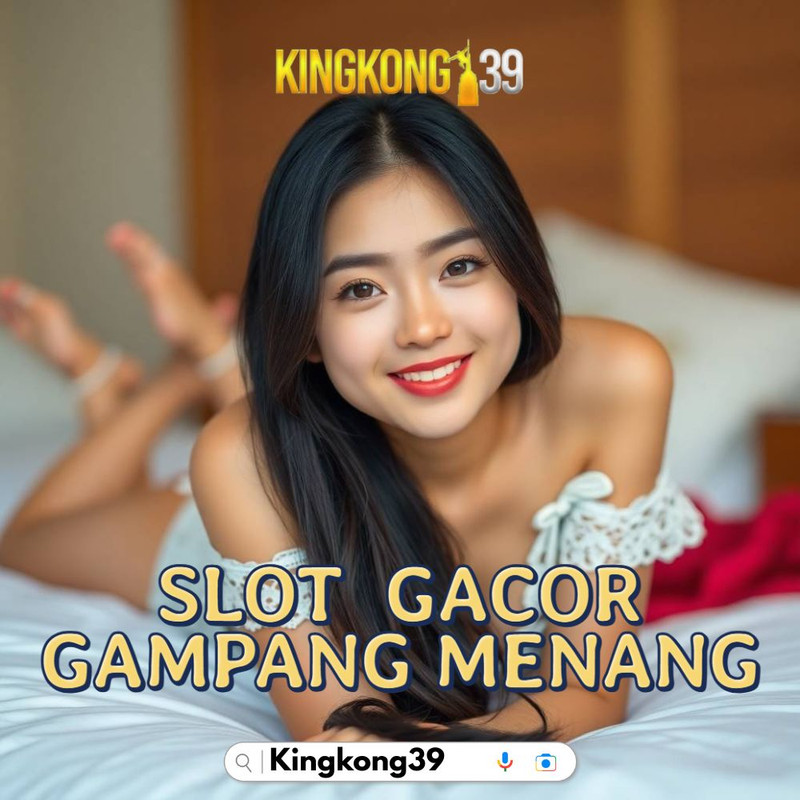
Psst, hey! Sudah siap menjadi raja permainan slot? Diam-diam, aku punya rahasia yang bakal buat kamu mampir ke puncak leaderboard tanpa keringat dingin. Yup, kamu nggak salah dengar. Di Kingkong39, kami mempunyai kunci-kunci kemenangan yang bakal membuat sesama pemain slot online iri hati. Penasaran? Simak tips menang slot hoki berikut ini!
Pertama dan terpenting, kenali mesin slot yang kamu mainkan. Setiap mesin punya karakteristik berbeda, dan di Kingkong39, kami punya koleksi yang akan membuatmu terkesima. Jadi, mulailah dengan memilih mesin yang paling sesuai dengan style permainanmu. Apakah kamu tipe yang suka tantangan tinggi atau yang lebih main aman? Pilihan ada di tanganmu!
Kedua, jangan lewatkan bonus dan promosi yang ditawarkan Kingkong39. Seringkali, para pemain mengabaikan aspek penting ini. Kami menawarkan berbagai bonus yang bisa meningkatkan peluang kemenanganmu, jangan sia-siakan kesempatan emas ini!
- Manfaatkan bonus sambutan - Ideal untuk mendapatkan start yang kuat.
- Pergunakan putaran gratis - Peluang ekstra tanpa mengeluarkan biaya tambahan.
- Ikut serta dalam turnamen - Hadapi pemain lain dan rebut hadiah besar.
Ketiga, atur bankrollmu dengan bijak. Ini bukan hanya tentang berapa banyak yang kamu menangkan, tapi juga berapa banyak yang bisa kamu pertahankan. Di Kingkong39, kami memberi kamu alat untuk mengelola keuanganmu dengan cerdas, memastikan bahwa kamu bermain dalam batas dan meningkatkan peluang untuk menang.
Terakhir, tetap santai dan nikmati permainan. Ingat, slot online bukan hanya tentang menang, tapi juga tentang menikmati setiap momen permainan. Di Kingkong39, kami percaya bahwa ketika kamu menikmati permainan, kemenangan akan mengikuti secara alami.
Siap untuk membuktikan keberuntunganmu? Bergabunglah dengan para pemain beruntung lainnya di Kingkong39 dan putar roda keberuntunganmu hari ini. Dengan tips menang slot hoki ini, kamu tidak hanya akan bersenang-senang — kamu juga bisa meraih kemenangan besar! Kunjungi kami sekarang juga dan jadilah bagian dari kisah sukses Kingkong39!